In collaboration with researchers from Ulm and Neuchâtel, Empa will soon be examining material samples on board the ISS. These are super-hard, corrosion-resistant alloys based on palladium, nickel, copper and phosphorus – also known as “metallic glasses”. A high-tech company from La Chaux-de-Fonds, which manufactures materials for the watchmaking industry, will also be on board.
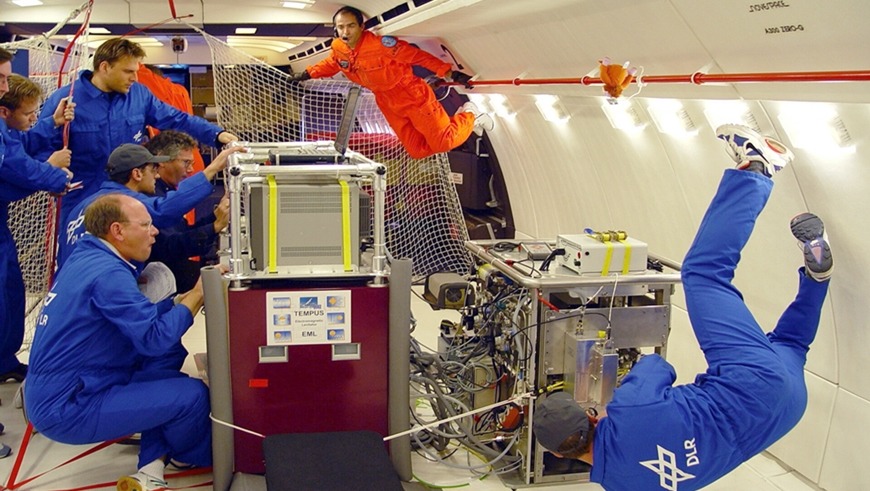
Weightless for a few seconds: Scientists from the University of Ulm during a fusion test in the Zero-GAirbus operated by Novespace. Image: Airbus Defence and Space
It has the color of white gold, but is as hard as quartz glass and at the same time highly elastic. The smooth surface is free of crystalline structures and makes the material resistant to salts and acids. One-off parts – for medical implants, for example – can be manufactured by 3D printing, while large series – for watch cases, for example – are produced by injection molding. That’s pretty much how we describe the dream material that scientists are currently researching. This is “metallic glass”.
Antonia Neels, head of Empa’s X-ray Analysis Center, has been working on this mysterious material for some fifteen years. His team studies the internal structure of metallic glass using a variety of X-ray methods, discovering links with properties such as deformability and fracture behaviour. Even for materials science professionals, metallic glasses are a headache: “The closer we look at the samples, the more questions arise,” explains Antonia Neels. The ambition of the researchers is all the greater.
Together in space
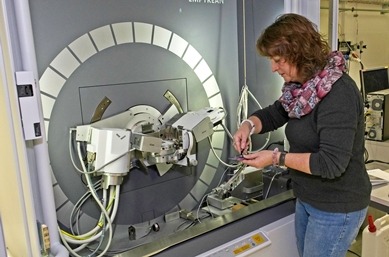
Antonia Neels, a researcher at Empa, is an expert in metallic glasses and will be analyzing samples from the ISS. Image: Empa
In a few months’ time, a sample of metallic glass will be examined in microgravity on the International Space Station (ISS). A group of researchers, with the participation of Empa, prepared the samples and registered them with the European Space Agency (ESA) for space flight. The special alloy is supplied by the PX Group of La Chaux-de-Fonds, which manufactures materials for the watchmaking and dental technology industries. The team also includes researchers Markus Mohr and Hans-Jörg Fecht from Ulm University’s Institute of Functional Nanosystems, and Roland Logé from EPFL’s Laboratory of Thermomechanical Metallurgy in Neuchâtel.
The manufacture of metallic glass is not so simple: compared to window glass, specially selected metal alloys have to be cooled up to a hundred times faster to prevent the metal atoms from assembling into crystalline lattices. Only when the melt solidifies extremely rapidly does it form a glass. In industry, thin sheets of metallic glass are produced by pressing the molten mass between copper rollers rotating at high speed. Researchers sometimes cast their samples in molds made of solid copper, which dissipates heat particularly well. But these methods do not allow us to produce larger, more massive pieces in metallic glass.
3D printing can help
One possible solution to this dilemma is 3D printing using the powder bed method. A fine powder of the desired alloy is heated for a few milliseconds by a laser. The metal grains fuse with their neighbors to form a kind of foil. A thin layer of powder is then placed on top, and the laser fuses the freshly deposited powder with the underlying foil, gradually creating a three-dimensional part from numerous grains of briefly heated powder.
This method requires fine dosing of the laser pulse. If the laser burns the powder too weakly, the particles do not fuse together and the part remains porous. If the laser burns too hot, it melts the lower layers again. This repeated melting allows the atoms to reorganize and form crystals – and that’s the end of metallic glass.
X-ray methods
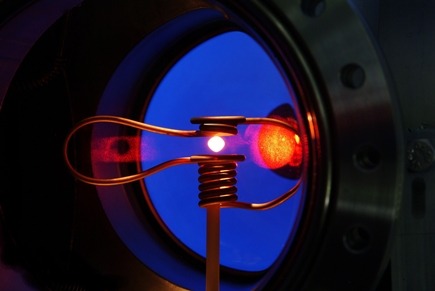
Space laboratory: In 2014, astronauts installed the electromagnetic levitator (EML) on the ISS. In this device, glass droplets float for longer. Image: ESA
Antonia Neels’ team at Empa’s X-ray Analysis Center has already analyzed several such samples from 3D printing experiments. The results always raise new questions. “There is some evidence that the mechanical properties of glasses do not deteriorate, but rather improve when the sample contains small crystalline fractions,” explains Antonia Neels. “We’re now looking at the question of what proportion of these crystals should be in the glass, and what type of crystals should form to increase, for example, the flexibility or impact resistance of glass at room temperature.”
To trace the growth of crystals in an otherwise amorphous environment, Empa’s experts use various X-ray methods. “With radiation of different wavelengths, we can learn a little more about the structure of the crystalline parts, but also determine the near-order phenomena of the atoms in the sample – in other words, determine the properties of the chemical bonds,” explains Neels. In addition, X-ray imaging analysis, known as micro-CT, reveals information about density variations in the sample. This indicates phase separation and crystal formation. However, the density differences between the glassy and crystalline zones are minute. Detailed image processing is therefore required to visualize the three-dimensional distribution of crystalline parts.
Parabolic flight in an Airbus
But the material samples produced by the 3D laser printer are not enough to fully solve the enigma of metallic glass. “We need to know at what temperatures these crystals form, how they grow – so we can define stable manufacturing processes,” explains X-ray specialist Neels. The thermo-physical parameters of the melt, such as viscosity and surface tension, provide important information. Experiments carried out on the ISS provide ideal conditions for these analyses. Preliminary experiments are taking place during parabolic flights.
From 2019, the first droplets of metallic glass floated on a trial basis. A specially equipped Novespace Airbus A310 carried out a microgravity flight with a material sample. Scientists from Ulm and a small metallic glass droplet from La Chaux-de-Fonds-based PX Group were on board. The metallic glass studied by the research group is composed of palladium, copper, nickel and phosphorus. In the TEMPUS (crucible-free electromagnetic process in microgravity) experiment, the glass droplet was held in suspension by a magnetic field and inductively heated to 1500 degrees Celsius. During the cooling phase, two short pulses of induction current vibrated the glowing droplet. A camera recorded the experience. After landing, the material sample was analyzed at Empa’s X-ray Analysis Center.
Why go to the ISS?
Analysis of the video of the parabolic flight allows conclusions to be drawn about the viscosity and surface tension of the droplet – important data for better control of the manufacture of metallic glasses with specific properties. But the period of microgravity during the flight lasts only 20 seconds – too short for detailed analysis. This is only possible on the ISS.
A sample of the same material has now been registered for a flight in the European COLUMBUS module on the ISS. The ISS-EML electromagnetic levitation furnace has been installed here since 2014. Each time, 18 samples of material travel with it, are automatically exchanged and can be observed by researchers on Earth via a video feed. The next batch of samples will take Swiss metallic glass into space.
Towards new processes
Using the much more detailed data from the space flight, the researchers aim to generate a computer simulation of the melt. All the answers will be brought together in a single model thanks to a combination of experiments on Earth and in space: What is the viscosity and surface tension at what temperature? When do crystals of what composition, size and orientation form? How does this internal material structure influence the properties of metallic glass? Based on all these parameters, the researchers intend to develop a manufacturing method in collaboration with industrial partner PX Group, so as to be able to produce the coveted material in a defined form. In the years to come, materials researchers from all the teams involved will still have a lot to do.
Source : Empa