The metallurgical industry generates numerous environmental impacts, including direct and indirect energy consumption from various sources, such as water, electricity, gas and effluent production. As a responsible manufacturer, Swiss Profile is aware of the importance of acting to minimize the environmental impact of its activities, wherever economically and technically possible. That’s why, over the past decade, the company has carried out several key projects and investments to reduce its carbon footprint.
A sustainable and economical approach to gaz for heat treatment
Heat treatment is a key stage in the production process. It requires the use of gases such as nitrogen and hydrogen, mainly for annealing or quenching stainless steel. With traditional gas supply methods, such as liquid or bottled nitrogen, users have to bear hidden costs such as rental fees, filling and delivery surcharges, order processing fees and environmental costs. To reduce these costs, Swiss Profile implemented an agile, eco-responsible solution: to produce nitrogen, the main component of air, from compressed air available on production sites.
With this sustainable, energy-efficient approach, the company produces its own nitrogen directly on site, using two generators to supply pure, clean, dry nitrogen gas. Thanks to this method, Swiss Profile has been able to eliminate regular deliveries by large trucks, thereby reducing the impact on road traffic and significantly reducing its carbon footprint.
This measure ensures constant supply, without ever having to worry about delivery delays. As a result, the risk of service interruption is greatly reduced, contributing to full customer satisfaction over the long term. With the implementation of this production process, the company also controls its own purity levels. The generators produce pure nitrogen from 99.5% to 99.999%, or anywhere in between.
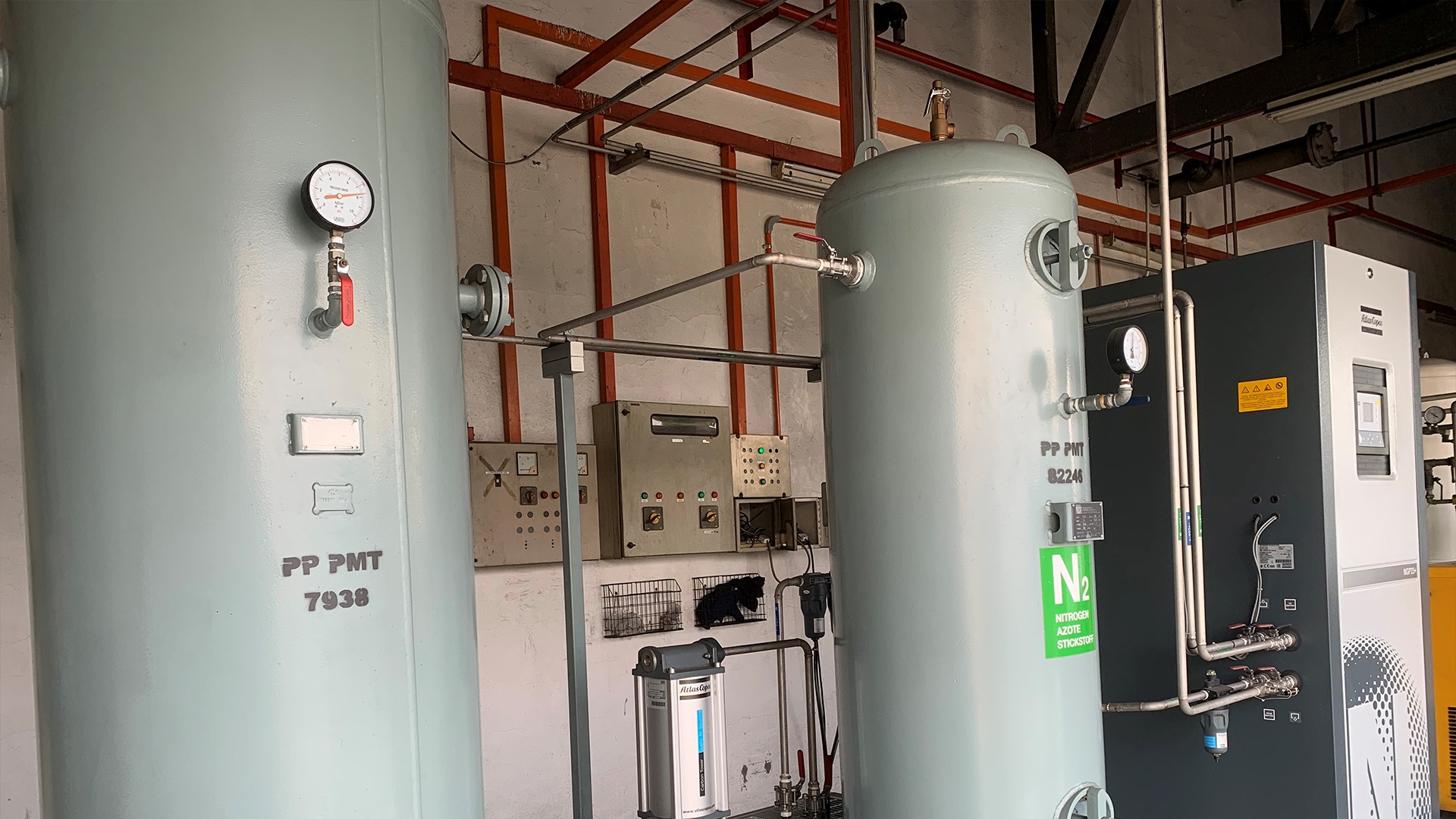
A system for recyclingfrom chemical treatment
Water is a particularly precious resource. It is essential to Swiss Profile’s production processes, mainly acid pickling or tumbling and detergent degreasing, which generate different types of wastewater. The volume of water in this wastewater is 100 to 150 times greater than the volume of the chemical solution, thanks to the constant supply of fresh water for washing and rinsing in the final stage of the chemical treatment process.
To protect this resource, the company has implemented a wastewater and industrial effluent treatment solution based on vacuum evaporator technology. The technique transforms effluent into two streams, one of concentrated waste and the other of high-quality water. The evaporator operates under vacuum, so the boiling temperature of the liquid effluent is lower, saving energy and improving efficiency. The system recycles treated wastewater for reuse in production. The recycling process creates a valuable by-product that recovers and utilizes up to 90% of the volume treated. Once again, this measure will eliminate the need for trucks to collect tons of wastewater. Thanks to the use of a vacuum evaporator, Swiss Profile reduces the volume of effluent to be disposed of by 75%.
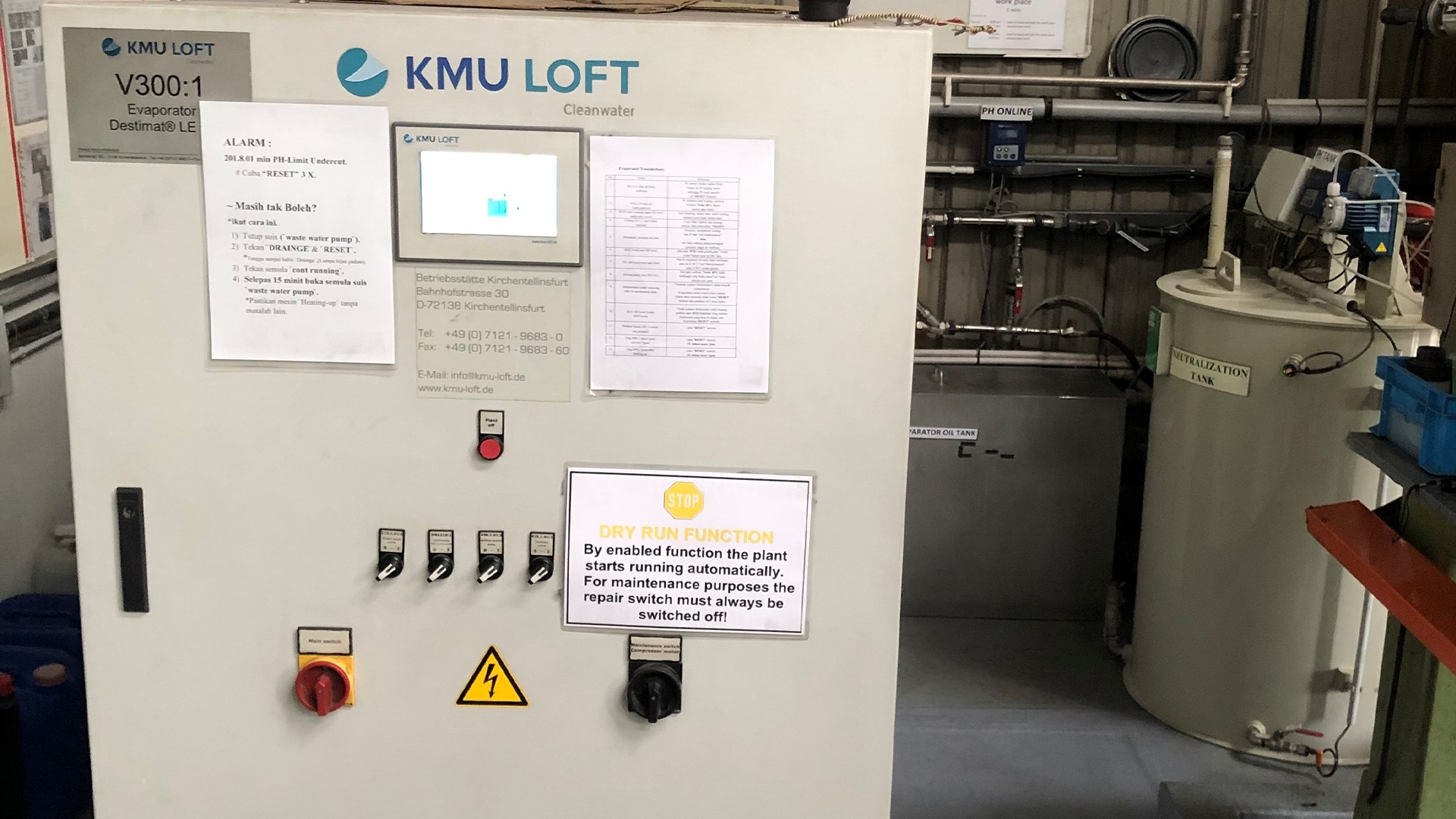
Strong initiatives to minimizing environmental impact
As a responsible manufacturer, Swiss Profile is committed to minimizing the environmental impact of its installations. Calling practices “ecological” or “sustainable” has become all too commonplace. We can even talk about standard. On the other hand, taking concrete steps to reduce consumption and our carbon footprint is a way of putting our money where our mouth is, and working to reduce our dependence on suppliers and contractors. By producing nitrogen and treating wastewater directly on site, we can increase efficiency in an economically viable way. These initiatives clearly demonstrate the company’s commitment to environmental responsibility and optimizing profitability.